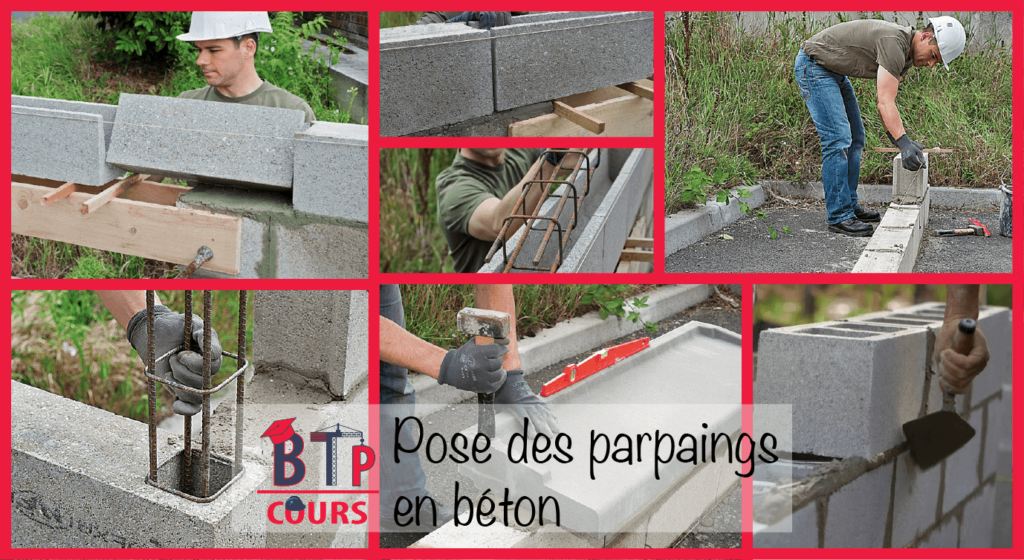
Table of Contents
Sommaire
01- Caractéristiques des ouvrages avec des blocs creux de béton vibré
- Résistance et Stabilité structurelle
- Isolement thermique
- Isolement acoustique
- Isolement hydrofuge et durabilité
- Résistance au feu
- Rapidité et Économie
02- Maille de pose
03- Préparation des fondations
04- La première rangée
05- Comment faire un bon mortier pour le hourdage
- Matériaux
- Mélange
06- Guide pour choisir un type de mortier – dosification
07- Mortier de rejointoiement
- Cône d’Abrams
08- Maintenir les blocs au sec
09- Éviter les ponts hydrauliques avec le mortier
10- pose des blocs
11- Niveau – alignement – verticalité
12- Joints horizontaux et verticaux – terminaison
- Joints
- Les joints saillants sont à éviter
- Terminaison superficielle
13- Joints de dilatation
14- imperméabilisation des blocs restant apparents
- Hydrofugeants qui pénètrent dans la superficie (Photo test A, à gauche)
- Hydrofugeants qui forment une pellicule sur la paroi (Photo test B à droite)
- Quoi choisir ?
- Les crépis
01- Caractéristiques des ouvrages avec des blocs creux de béton vibré
Résistance et Stabilité structurelle
La propre capacité portante du propre BLOC Creux, ajoutée à la possibilité d’incorporer des ferraillages en quantités et endroits critiques, arrivent à satisfaire un large spectre d’exigences face à la résistance et stabilité des structures des murs hourdés.
Isolement thermique
Isolement acoustique
Isolement hydrofuge et durabilité
Résistance au feu
Rapidité et Économie
02- Maille de pose
On peut aussi utiliser des:
- parpaing plein 15x20x50
- parpaing 10 cm
- parpaing creux 20x20x50
- parpaing creux 15x20x50
- parpaing 10x20x50
- parpaing 15x20x50
- parpaing 20x20x50
- parpaing plein 20x20x50
- agglo 20x20x50
03- Préparation des fondations
04- La première rangée
05- Comment faire un bon mortier pour le hourdage
Matériaux
Mélange
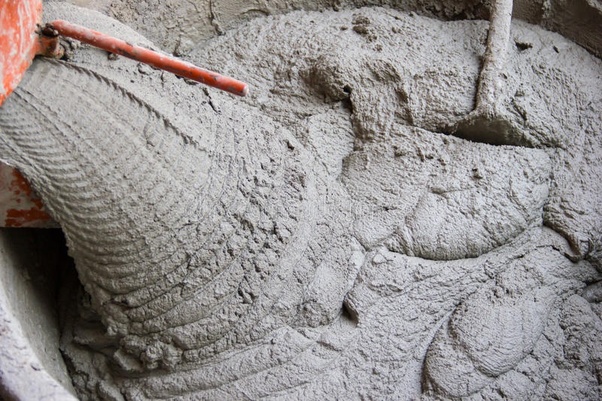
06- Guide pour choisir un type de mortier – dosification
Table 1: Sélectionner le type de mortier selon la fonction du mur
Mortier type | Fonction du mur |
A | Murs et Semelles de fondation, murs porteurs extérieurs de fortes charges de compression ou charges horizontales générées par poussées du sol, vents ou séismes |
B | Murs porteurs, ayant seulement des charges de compression mais qui requièrent des hautes résistances d’adhérence des charges de compression pour des efforts de cisaillement ou flexion. |
C | Murs porteurs ou extérieurs de charges moyennes. |
D | Cloisons intérieures non porteuses. Cloisonnement décoratif. |
Table 2: sélectionner la dosification recommandée (en volume)
Mortiers | Proportions de matériels agglomérant (en volume) | |||
Ciment portland | Ciment de maçonnerie | chaux | ||
Ciment et chaux | A | 1 | – | 1 / 4 |
B | 1 | – | 1 / 4 a 1 / 2 | |
C | 1 | – | 1 / 2 a 1 / 25 | |
D | 1 | – | 1 , 25 a 2,5 | |
Ciment de maçonnerie | A | 1 | 1 | – |
B | 1 /2 | 1 | – | |
C | – | 1 | – | |
D | – | 0,8 | – |
07- Mortier de rejointoiement
Cône d’Abrams (cone de chantier)
- Plastique de 5 à 9 cm,
- Très Plastique de 10 à 15 cm,
- Fluide à partir de 16 cm.
Table 3 : dosifications pour mortiers de remplissage
Type | Ciment Portland | Sable | Agrégats grossiers |
Béton de remplissage | 1 | 2 1 / 4 – 3 | 1 – 2 |
Mortier de remplissage | 1 | 1 1 / 4 – 2 | 0 |
08- Maintenir les blocs au sec
09- Éviter les ponts hydrauliques avec le mortier
10- pose des blocs
11- Niveau – alignement – verticalité
12- Joints horizontaux et verticaux – terminaison
Joints
Les joints saillants sont à éviter
Terminaison superficielle
13- Joints de dilatation
14- imperméabilisation des blocs restant apparents
Hydrofugeants qui pénètrent dans la superficie (Photo test A, à gauche)
Hydrofugeants qui forment une pellicule sur la paroi (Photo test B à droite)
Quoi choisir ?
Les crépis
Pose de brique agglos
Mot clés: Pose de briques, maçonnerie parpaing, gros oeuvre, dimension parpaing 10, parpaing plein 15x20x50, parpaing plein 15x20x50, parpaing 10 cm, parpaing creux 20x20x50, parpaing creux 15x20x50, parpaing 10x20x50, parpaing 15x20x50, parpaing 20x20x50, parpaing plein 20x20x50, agglo 20x20x50, devis isolation thermique, isolation des combles, devis isolation, beton mortier, beton proportion, sac beton, poids sac ciment
p.p1 {margin: 0.0px 0.0px 0.0px 0.0px; font: 12.0px Helvetica; color: #454545}
p.p2 {margin: 0.0px 0.0px 2.0px 0.0px; font: 14.0px Helvetica; color: #454545}
p.p3 {margin: 0.0px 0.0px 2.0px 0.0px; text-align: center; font: 14.0px Helvetica; color: #454545}
p.p4 {margin: 0.0px 0.0px 0.0px 0.0px; text-align: justify; font: 12.0px Helvetica; color: #454545}
p.p5 {margin: 0.0px 0.0px 0.0px 0.0px; text-align: justify; font: 12.0px Helvetica; color: #454545; min-height: 14.0px}
p.p1 {margin: 0.0px 0.0px 0.0px 0.0px; font: 12.0px Helvetica; color: #454545}
2 Commentaires
Bonsoir monsieur ! Je suis dans le domaine et je voudrais vous demander si vous pouviez m'envoyer le document complet de métré
Bonjour j aimerai bien avoir le document, si vous pouvez me l envoyer s il vous plait