5,8K
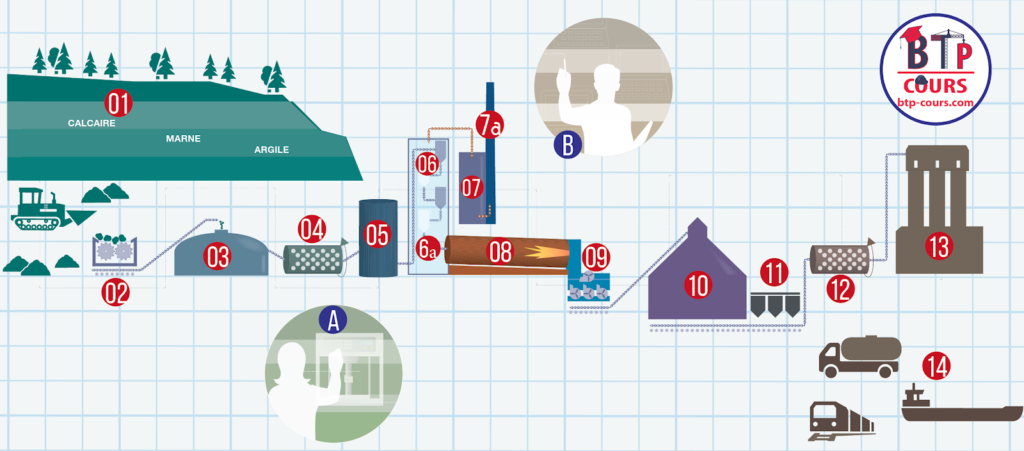
Table of Contents
la fabrication du ciment process & transports
Dans cet articles je vous présente les étapes de fabrication du ciment
Étape : 1
Extraction des matières premières.
Étape : 2
Concasseurs primaires & secondaires : réduisent les matières premières en éléments d’une dimension maximale de 150 mm.
Étape : 3
Hall pré-homogénéisation : mélange les matières premières de manière à obtenir une composition homogène.
Étape : 4
Broyeur sécheur du cru : broyage de la matière première en une farine très fine, le « cru ». Pour fournir tous les constituants minéraux nécessaires à la production du clinker – fer (Fe2O3), alumine (Al2O3), ou silice (SiO2) – on peut y ajouter de faibles proportions de matières naturelles (bauxite, oxyde de fer, schiste, argile ou sable), ou de déchets minéraux de composition chimique identique.
Étape : 5
Silo d’homogénéisation du cru.
Étape : 6
Tour de préchauffage + Précalcinateur : en passant par cette tour, le cru va atteindre une température de 900 °C, grâce au flux de gaz chauds sortant du four qui remontent la tour à contre-courant. C’est là que débute la décarbonatation, réaction qui détache des molécules de CO2 contenues dans le calcaire, le transformant en chaux. Certaines cimenteries sont équipées d’un précalcinateur 6a , foyer complémentaire dans la partie inférieure de la tour.
Étape : 7
Filtre à manche : filtre les poussières des gaz sortant du four avant leur passage dans la cheminée 7a .
Étape : 8
Four rotatif : le cru préchauffé pénètre dans ce tube (3-6 m large x 50×90 m long) légèrement incliné qui tourne sur lui-même, et progresse ainsi à travers des zones de plus en plus chaudes jusqu’à atteindre les 1 450 °C. Cette chaleur intense, générée par la tuyère où sont brûlés combustibles fossiles et déchets, termine la décarbonatation et provoque la transformation du cru en clinker.
Étape : 9 et 10
Refroidisseur + silo de stockage clinker : le refroidissement brutal du clinker par air soufflé finalise sa transformation. Il est stocké dans des silos sur site, et utilisé sur site au fur et à mesure des besoins de production ou envoyé vers des installations de broyage extérieures.
Étape : 11
Autres constituants : d’autres matières finement broyées(laitier de haut-fourneau, cendres volantes, schistes calcinés, calcaire, fumées de silice) peuvent être ajoutées à la composition finale, pour produire un ciment répondant à des besoins spécifiques. Cela réduit d’autant la teneur en clinker et les émissions de CO2 qui y sont associées.
Étape : 12
Broyeur ciment : le clinker et les constituants sélectionnés sont finement broyés avec du gypse pour régulariser le temps de prise du produit final, fine poudre grise appelée « ciment Portland ».
Étape : 13 et 14
Silos de stockage + transport du ciment : le ciment est stocké dans des silos puis expédié en vrac ou conditionné en sacs (25-35 kg). Pour ses livraisons, l’industrie cimentière cherche à favoriser les modes de transport à faibles émissions de CO disponibles sur le territoire. 2
A – Le laboratoire sur site analyse les échantillons de matières premières, constituants, combustibles, clinker et ciment prélevés tout au long du process pour garantir la conformité du produit aux normes en vigueur.
B – La salle de contrôle réunit tous les équipements – systèmes experts d’exploitation, circuits vidéos, résultats en ligne de stations d’échantillonnage – qui permettent de piloter la cimenterie.
Mot clés : faire du beton, four rotatif, preparation beton, processus de fabrication, ciment portland, béton, fabrication béton, comment faire du beton, cimenterie de la tour